Solidworks, Yes.
So in a real like test scenario like you said it's important for the fixtures to greatly exceed the strength of the component being tested.
BUT, in SolidWorks simulation express it will not calculate permanent deformation/plastic/nonlinear etc. so when you run a sim with a part that will obviously fail in real life that is not important, as the simulation continues beyond the yield strength of the part in question if applicable.
So in the case of the axle although it deformed in both testing scenarios all of the force is still being transmitted to he swingarm with out any of the real life "energy loss" associated with deforming/breaking a component.
You are still right that it is better to have the most accurate representation of the part possible but, as you can see in the original post of the bending test, Solidworks continues to calculate stress and deformation well beyond (and in some cases, many times" the Yield strength of the material.
I'm going to do a more complete model in the future, just wanted to make sure 2x1 box would be strong enough so I could move on to the finer points and worry about the optimization and bracing later.
Just one more comment, I don't really trust FEA in solidworks as fact, it's nice to get a ballpark (+/- 1 FOS) but when I was doing FEA on footpegs this morning it's pretty all of our footpegs have already broken off, and if you have aluminum pegs you wouldn't even be able to get on the bike. Food for thought.
You're making great points though! And don't quote me on this stuff. It's my hobby, not my job

EDIT!!!
In the interest of getting to the bottom of this I'm running new tests...
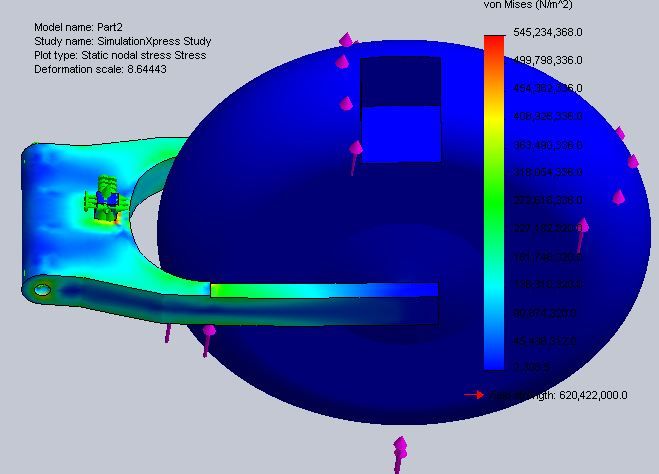
So with a beefier Axle and a wide hub this bending test came up considerably stronger, the whole part shows Factor of Safety > 1
and do the twist.
Stress
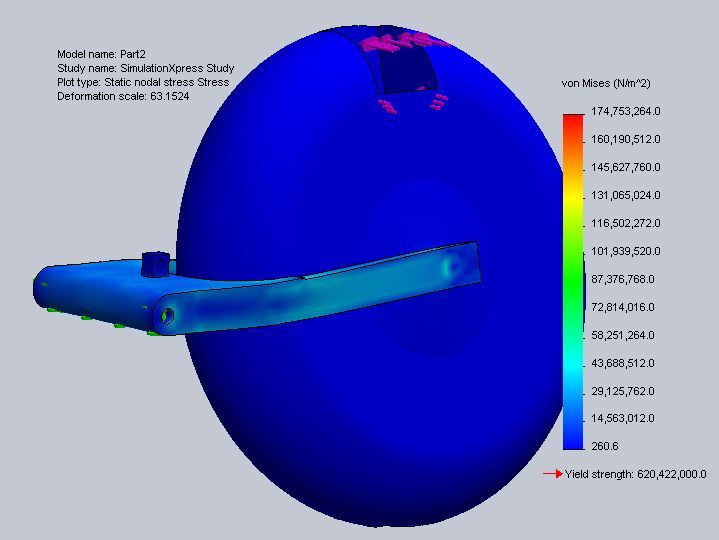
Displacement
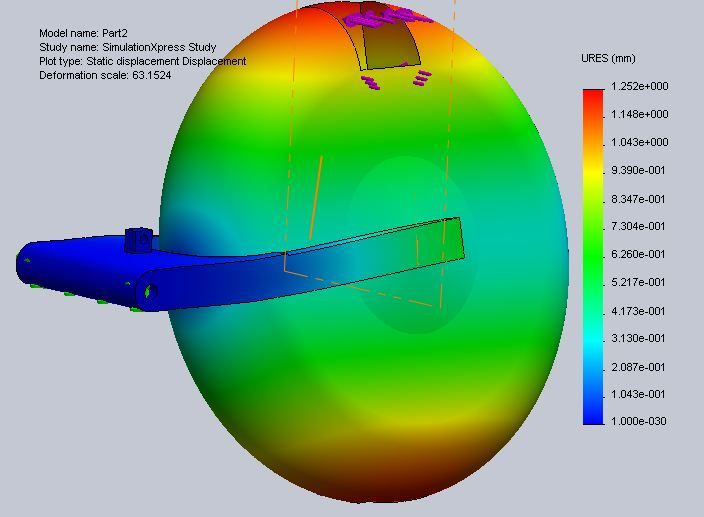
So now we've learned something about solidworks...
By beefing up the axle and the hub there is now a portion of the twist stress that is being countered by the axle, as it is a strong tube and most importantly
SOLIDWORKS SOLVES ONLY MERGED SOLID MODELS!
So although in real life the axle would slip around and wiggle in the slot, allowing the swingarm to bend independantly, in the solid model version it counts as a solid structural beam between the two sides, equivalent to having the back of the swingarm welded together.
That's why in the twist model there is a significant increase in strength, whereas in the bending model it is more moderate.
That's what i get from this anyways, more comments/opinions are welcome, cause at the end of the day nobody wants their parts to fail!
I guess if we're going to do this right we would resolve the moments into the ends of the swingarm and test the twist with....
oh f*ck it.
It's good
(at this point my spoked wheel would be a prickly, rubbery mess on the road behind me, oh well.)