First off let me say that I am by no means a chemist. If I had a chemistry class in High School, I don’t remember any of it.
This is a summary of what I’ve read.
Electroplating occurs in an electrolytic substance of free ions which are the carriers of electric current. Here this is, Epsom salts (magnesium sulfate) and Vinegar (acid). Connected to the positive of an electric power source an anode made of zinc, attracting negatively charged ions causing Oxidation. At the negative side of the power source is the cathode, attracting positively charged cations, moving ions away toward the anode. Here it provides electrons to the cations to convert them back to the parent metal (zinc). This process is called reduction.
In short, the zinc leaves the positive side and binds itself to the negative side.
Supplies:
Various measuring cups, postal scale for measuring by weight, copper pipe and wire, and a plastic tub.
Epsom salts (pharmacy section of your local grocery store)
White Vinegar (baking section of your local grocery store)
Zinc Sulfate (available online, reduces time and increases quality of the plating)
Karo brand corn syrup. (baking section of your local grocery store, contains glucose that acts as a brightener by keeping the zinc crystals in alignment)
Zinc Anode, (online or in home stores in desert climates as it’s used for evaporative (swamp) coolers)
A DC Power Supply, low amps (1A to 300mA).
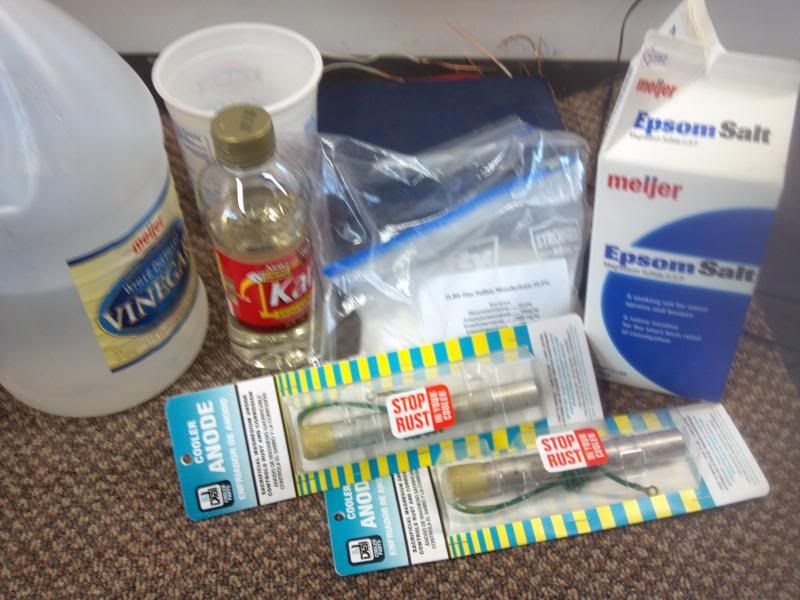
Solution:
4.5 liters water
300 grams Epsom salts
100 grams zinc sulfate
200ml of white vinegar
1/3 bottle of corn syrup
Stir in plastic tub till dissolved.
Setup:
Suspend Zinc Anode(s) in solution and hook up to positive of DC Power Supply.
Have copper bar go across top of the plastic tub, copper wires wrapped around bar, so you can suspend parts in solution without touching Zinc Anode(s).
Electro zinc plating:
Strip metal to be plated. I soaked my parts in vinegar for several days to dissolve the rust, and then cleaned with a wire brush and sand blasted. Finally I wiped my parts down with denatured alcohol.
My first try, this is a pivot shaft from the center stand of a 75 cb750 I'm restoring.
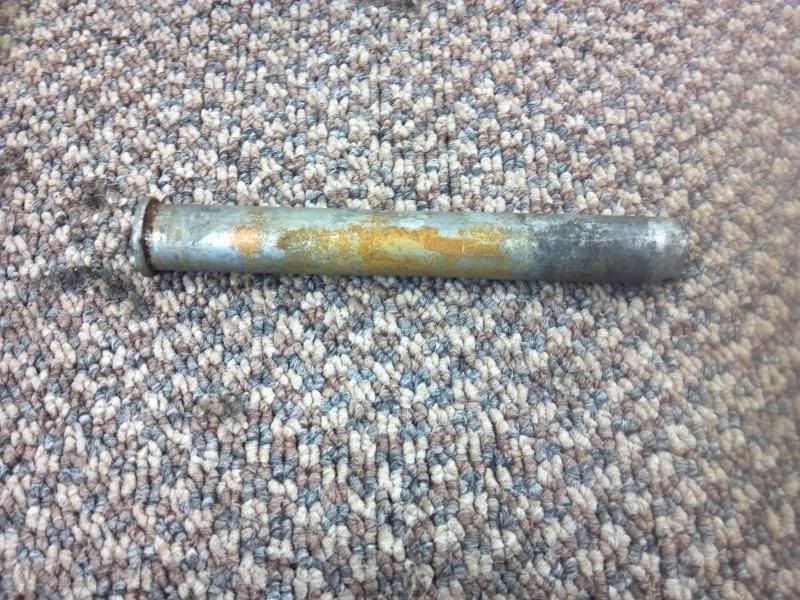
After sand blasting
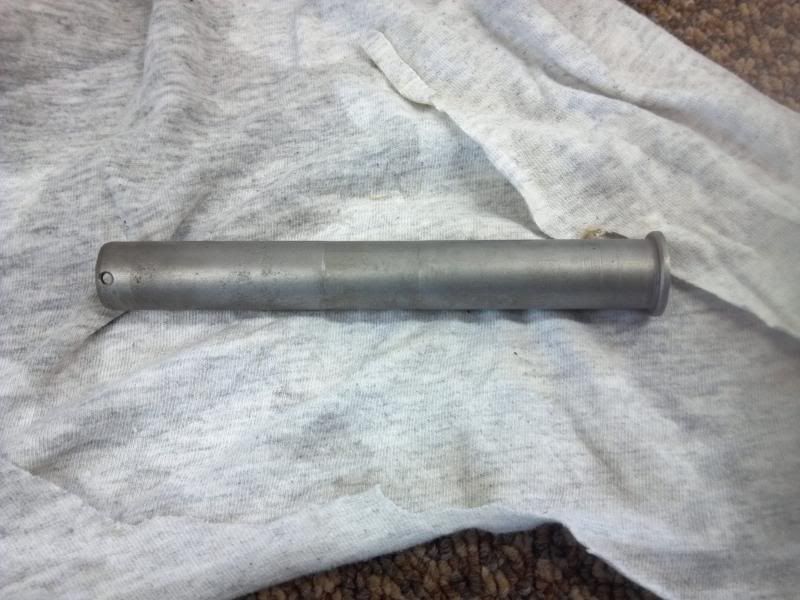
Suspend part in solution with copper wire.
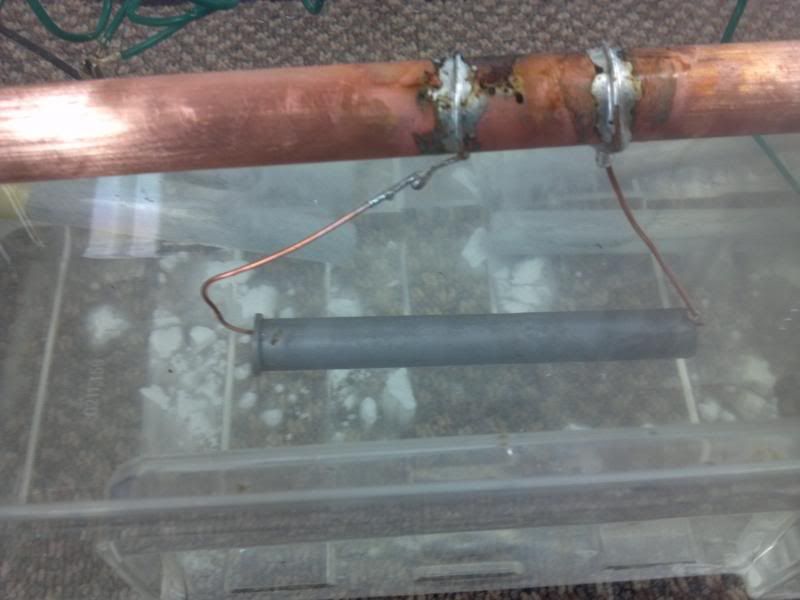
Attach negative power supply to copper bar.
In about 1 minute your Anodes and part will bubble.
In 5-10 minutes disconnect power and inspect part. It should have a milky coating of zinc. Clean with wire bush and/or steel wool.
You may need to repeat for a thorough covering.
Then polish to a shine.
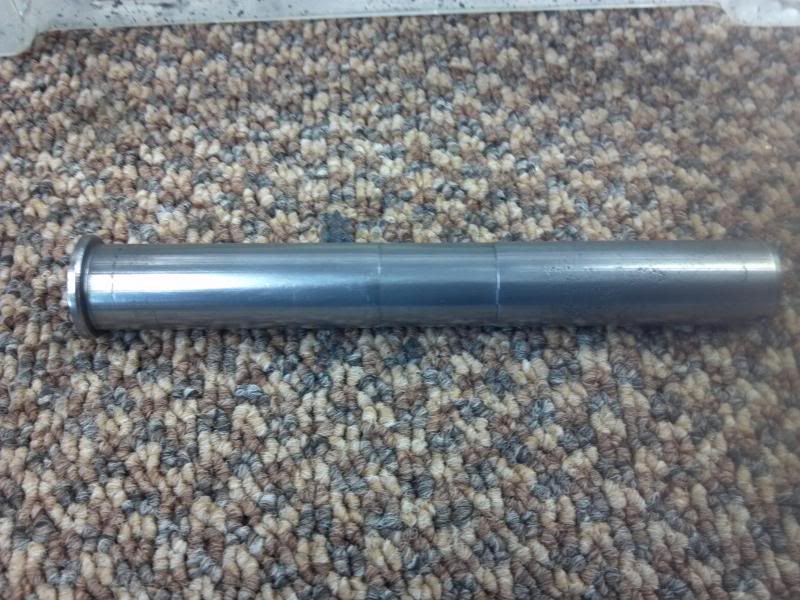
Some more parts, rusty engine mount bolts
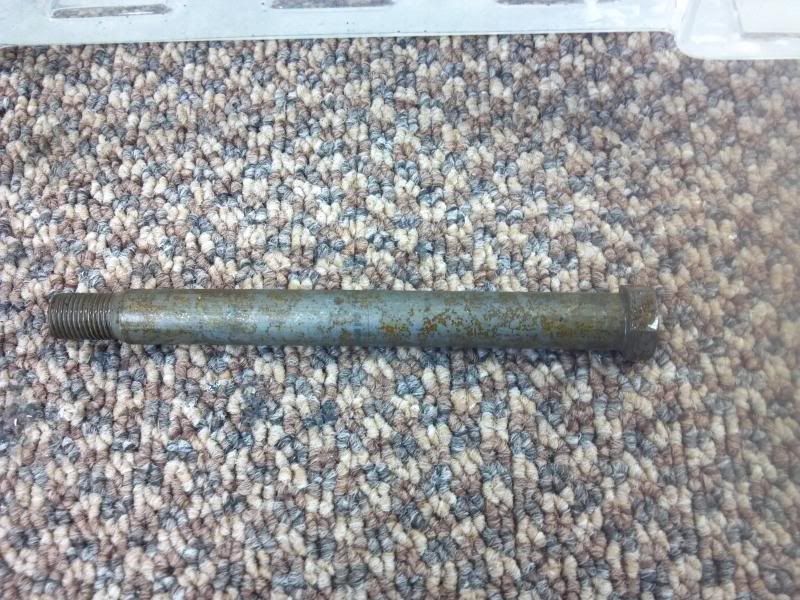
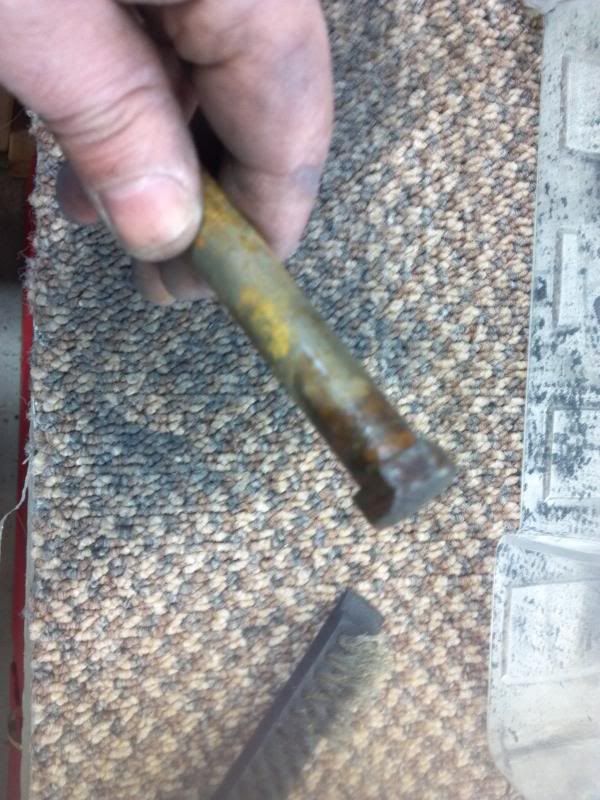
After plating and polishing
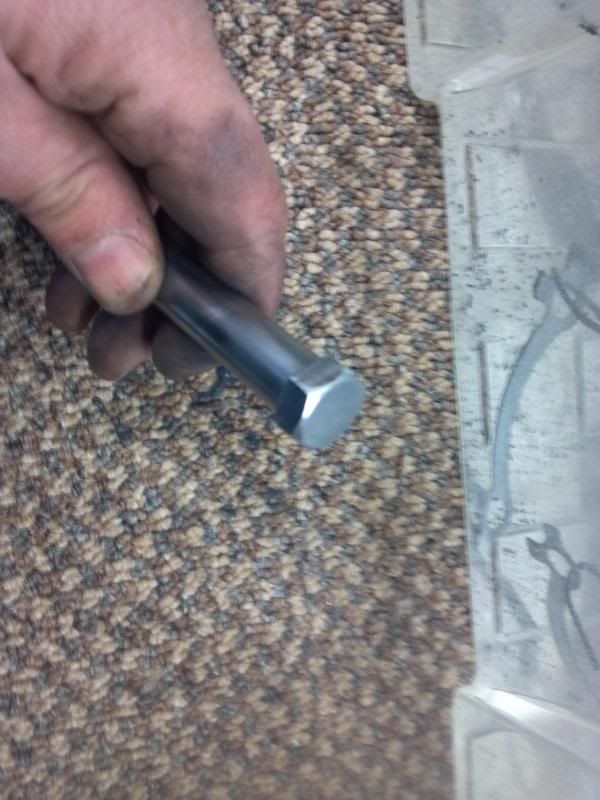
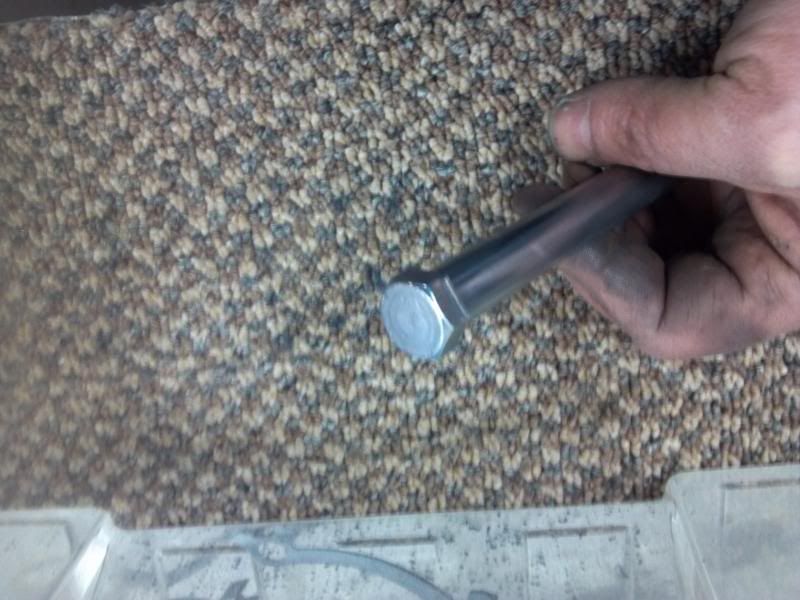
Part of the center stand, connects frame to spring.
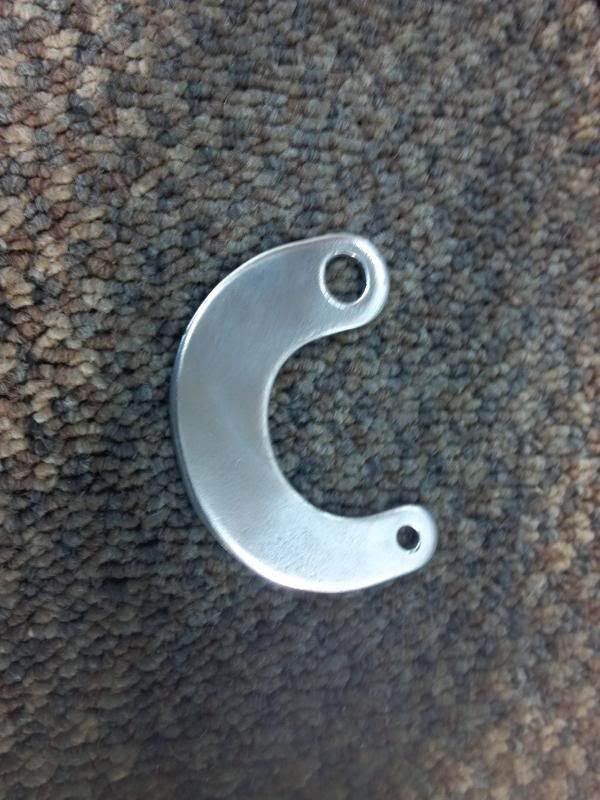
Rear brake arm
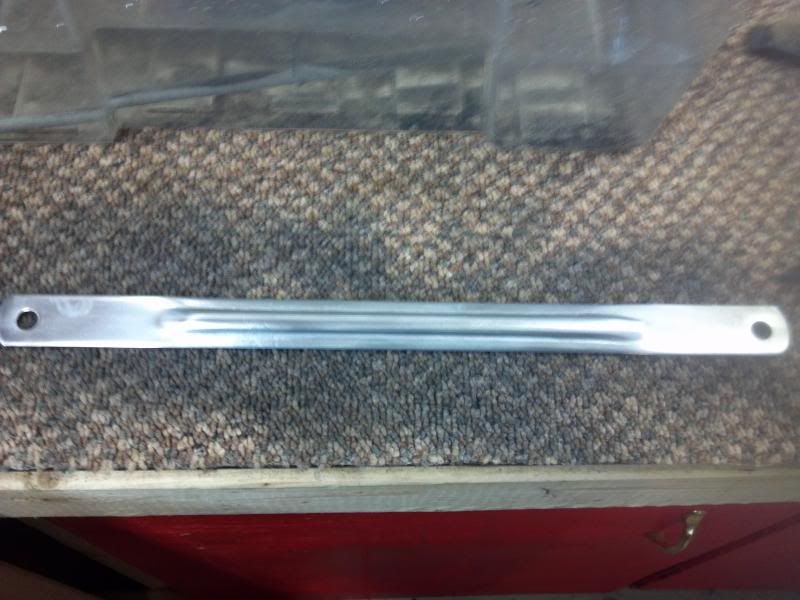
Head nut
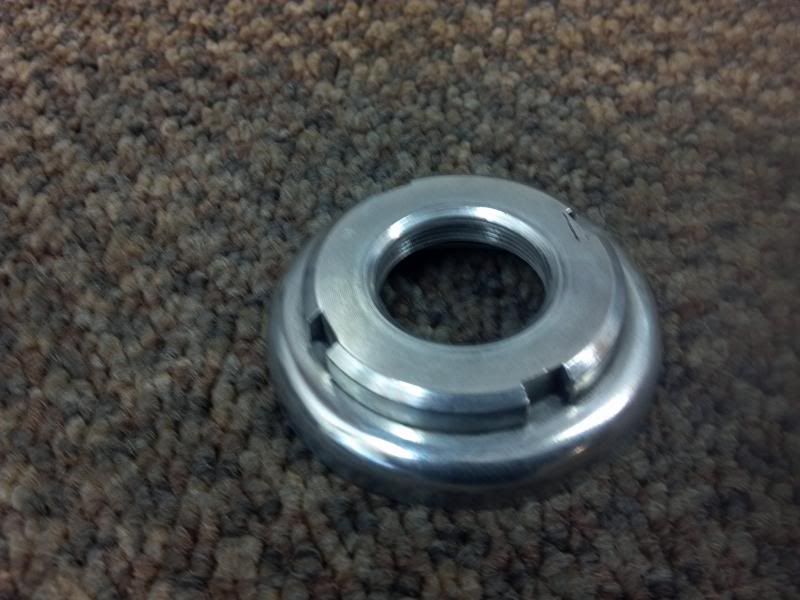
All the parts I did today.
All these parts are from a 1975 CB750K I'm restoring. All were dirty, rusty and pitted. Now plated to hold up to the elements of an other 40 years.:thumbsup:
This box of parts took me the better part of a day. The process is time consuming. I plan to buy common sized stainless steel nuts and bolts from the hardware store. But for the stuff that is specific to the bike, I plan to zinc plate.