Truing. Not as bad as I thought. Basically walked away from the lacing for a day or two. And started this when I could concentrate and was fresh.
Some key threads are inserted here. Thanks KONG. Your explanation worked best for my brain...and is repeated below so others dont need to search for it.
_____________________________
After you lace your wheels up - and don't worry about how the previous owner did it, you just do yours correctly - put your wheel in your truing stand and do the following. Starting at the air valve hole unscrew each nipple, lubricate it, and then tighten each nipple 10 turns, go all the way around. Take the wheel off the stand and shake it while holding by the rim, then set it into the stand and do the same thing again and go around and tighten each one 2 or 3 turns. Do that until each of them is still free to be easily turned but ever so slightly snug. Now its time to true the wheel.
Set up your indicator and begin by checking the wheel for roundness, don't worry about side wobble, just spin it and check the runout as the distance from axle center to edge of rim varies. You bring the wheel true this way first and you do it by pulling on the tall side. Spin the wheel and find the high spot, mark it with masking tape on the side of the wheel - then go exactly opposite of it and tighten the two spokes across from it by 1 turn each, the next two to each side of them by 1/2 turn, and the next two after them by 1/4 turn. Then spin and measure again. Do the same thing again if necessary but if you have to do it more than once you have to loosen the high side the same way as you tighten the low side. Never turn any spoke more than 1 turn at a time. Oh, somewhere on the rim there may be a hump where the ends were butt-welded together, ignore it. Keep adjusting the wheel until your readout is +/- 0.10 inch or better - and you should be able to do better.
Once you've got the wheel round you take the wiggle out of it. Set up your indicator to measure runout side to side and spin the wheel slowly and find the center of the section that is most distant from your side. Here you also should work about 4 or 6 spokes at a time, but do not make the adjustments so large (usually 1/2 turn at a time) and here as you tighten the spoke that feeds to the side of the hub nearest you you have to loosen the nipple for the spoke next to it on each side by the same amount. This part will go quickly, its a lot easier to do than it sounds. Make your adjustments until you have reduced the runout as noted above.
Finally once you have it right take the wheel out of the stand and find a soft surface and bounce it a few times, I just use a carpeted floor. Bounce it like hitting a small pothole. Then remount the rim in your truing stand and measure your runout again. Make corrections as necessary but this time only tighten the nipples, don't loosen any - the adjustments needed, if any, will be very small.
Now, finally, spin the rim and lightly tap each spoke with your spoke wrench as it passes by. Listen to the sound. Most will go clink, but a couple will go clunk. Tighten the clunkers about 1/2 turn at a time until they sing out like their sisters. Check runout one more time and if all is well check each nipple to see if any spoke-end is sticking out. If any are take a grinder and remove the protruding parts. Then put a new rimstrip on it and you're done.
__________________________________________
Another very helpful bit was from
http://www.webbikeworld.com/motorcycle-wheels/spoke-wheels/vertical Alignment
Some nice diagrams on this website that help with which way things move as you tighten or loosen.
Here is harbor freight stand
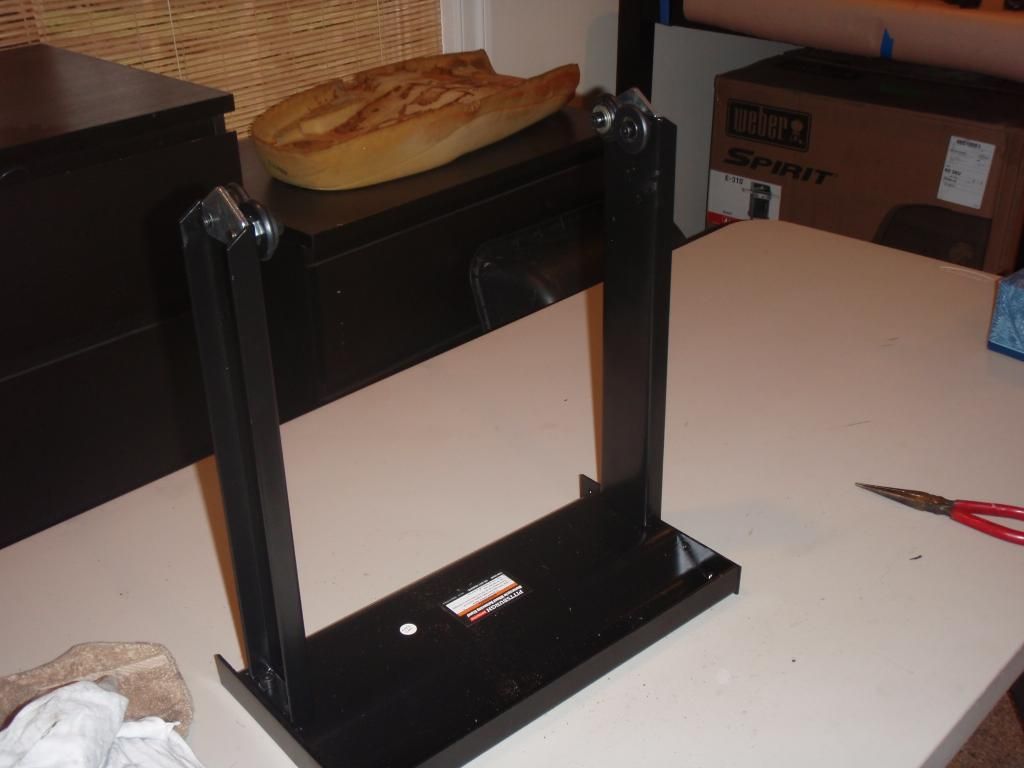
What I found out after finishing the front was that these little bearing surfaces were not round so the shaft actually wobbled.
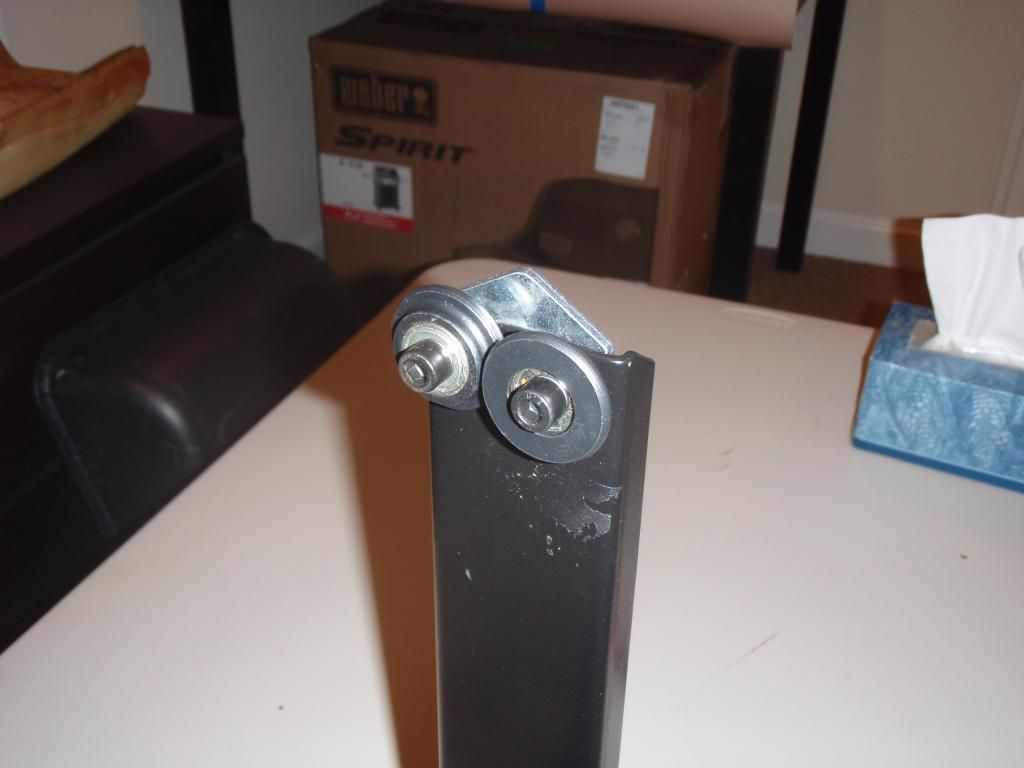
Works fine as a static balancer, but dont buy this as a truing stand. Yes, I know they don't advertise it as a truing stand and yes I was trying to cheap out.... You can true the wheel, but since the shaft wobbles on the stand, you are actually not true once on a straight bar such as your AXLES...DOH !
So I then used the bar (which was true the issue is the bearings on the HF stand). This is the setup between my bench and my drill press.
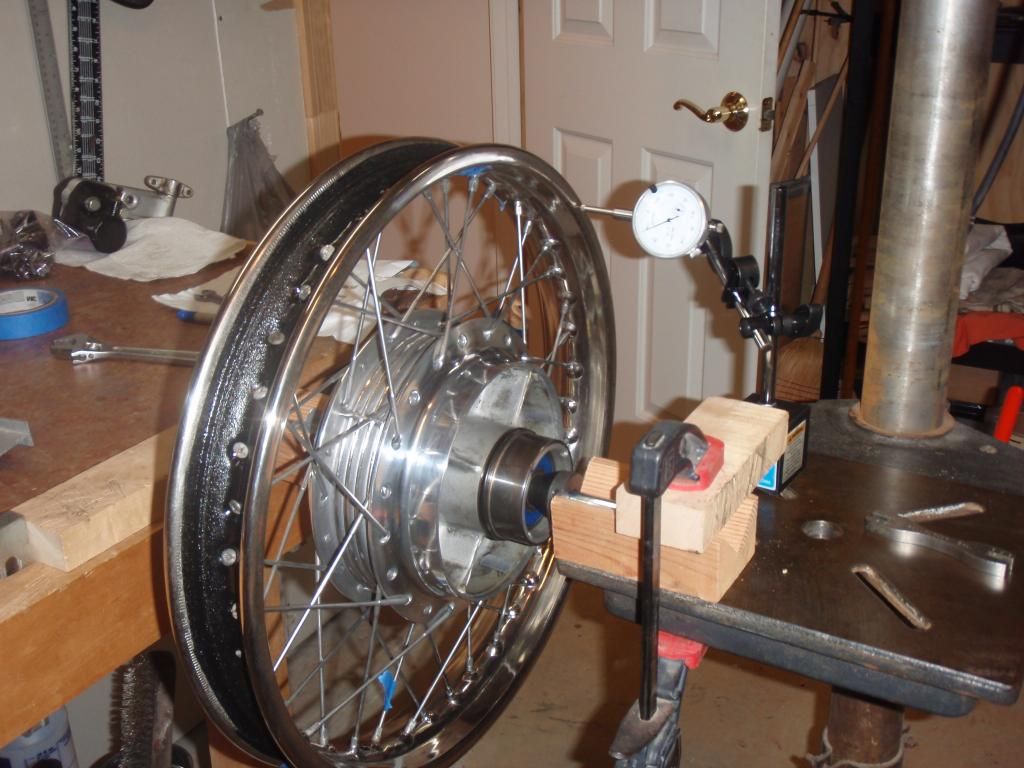
This worked perfectly. Follow the advice KONG and the link provided above. And soon you are true. It felt great to get it right. Took about 90 minutes per wheel once i got off the harbor freight stand. The last thing I did was hit each spoke with the spoke wrench and listen to the tone (sound). Any that were a dull low sound were loose. Snug those up and recheck to be sure it didnt drive out of position.
Also, mind the weld in the rim. This will never be a true spot and so don't chase that around and around. I taped it so I didn't panic each time the dial indicator jumped.