Santa came to my house early, with a sack-full of gearbox bits for the TriBSA

. Bearings, sleeves, bushes, springs, spacers, odds and sods in fact everything that needs replacing through wear or was just found to be missing in the first place.....
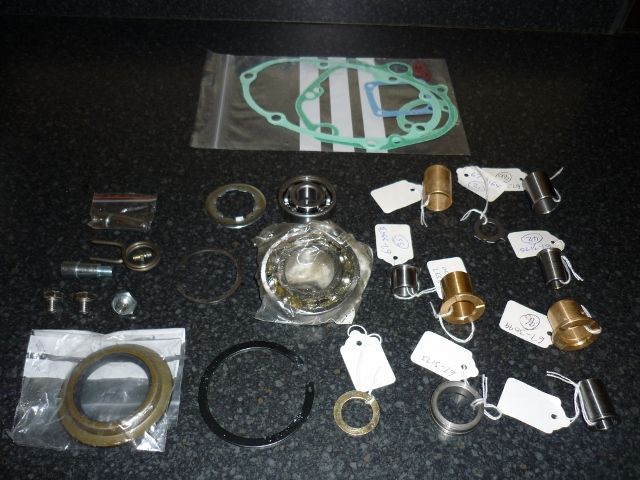
So in spite of the inconvenience and bad timing of Christmas festivities, I've had quite a productive couple of weeks. First job in the rebuild was to remove that drain plug, which had obviously made itself at home in there and was not going to go down without a fight. Patience, heat and perseverance won the day...
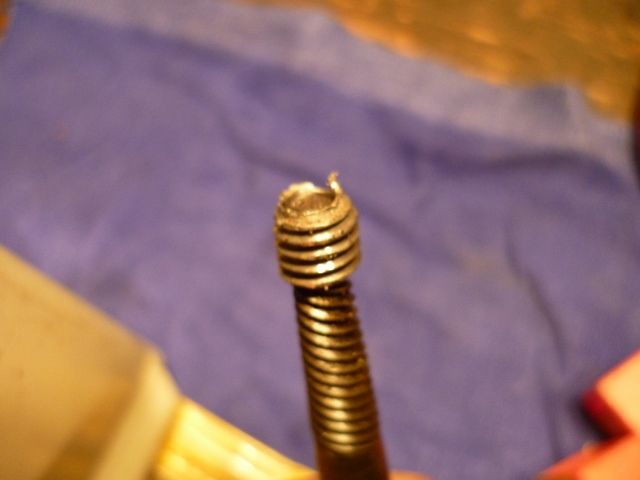
From then on it was just a case of 'rebuild is a reversal of the dismantling procedure', which makes it sound simple, which it wasn't. Replacement of the various bushes and sleeves required a bit of thinking about. Still sore from the whole tappet block episode, I measured each new piece against the old, just to satisfy myself that they would actually fit in the hole as they were supposed to. The layshaft bushes are drilled to correspond with oilways when they are pressed home, but the holes in the new ones were smaller than in the old ones. I opened them up because if I had fitted them slightly misaligned it could have blocked the oilways...
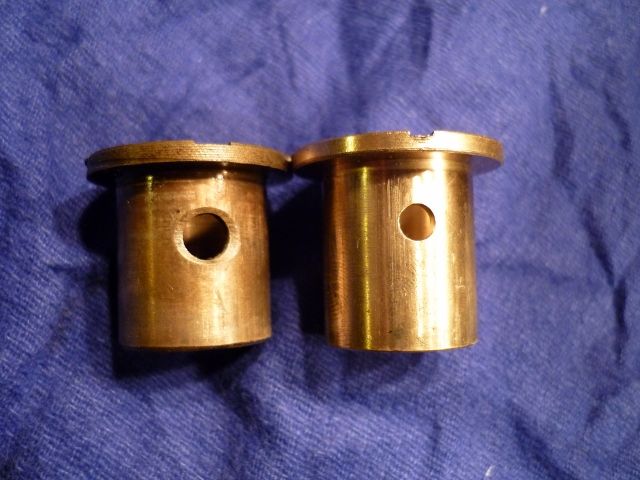

Pressing the bushes in and out of the cases was a right pain in the proverbial. I don't have a proper press, so I improvised. This involved me growing another hand as I juggled with various sockets and hot cases, trying to get it all lined up in the vice so the pressure was applied in the right spots without damaging the cases. This was a bit like playing Jenga, and on more than one occasion bits went flying across the garage as the whole lot slipped from position and I instinctively (and stupidly) tried to catch the falling bits, burning myself in the process. Idiot!

So here's the rear mainshaft bearing and layshaft bush installed. The new bearing comes shielded on one side, which if I'm very lucky might help to limit the amount of oil I'll see on the floor....
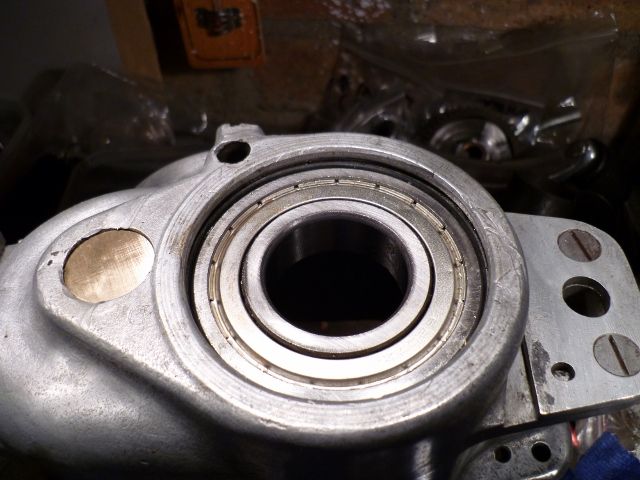
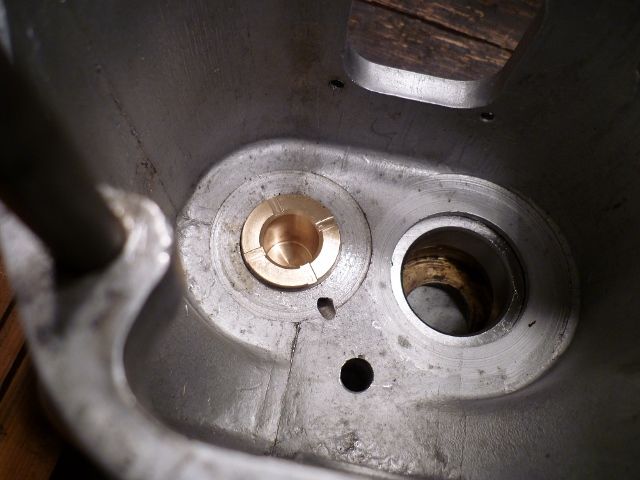
Although I bought new bushes for the sleeve gear, I ended up not using them. The interweb is rife with horror stories of blokes having replaced these, only for them to turn in use causing their drillings not to correspond with their oilways anymore, resulting in no lubrication and seized gearbox. There wasn't that much difference in slop between my old one and the new, so I let it be.
Sleeve gear fitted and new oil seal...
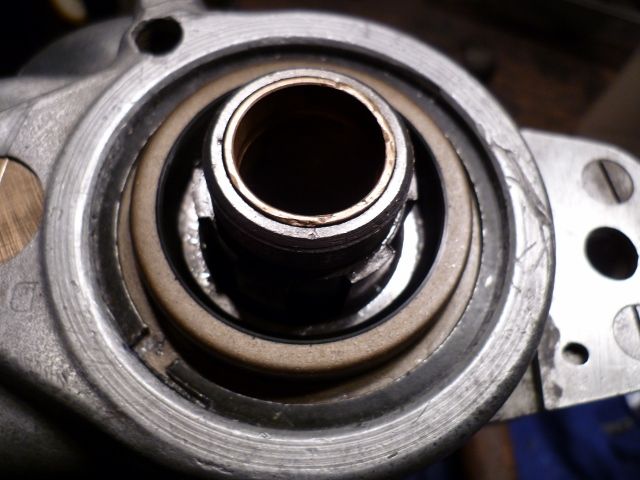
Tightening nut after replacing final drive sprocket, using an old chain in the vice and the wheel bearing retainer removal tool for my Norton, which just happened to be exactly the right size to locate in the two cutaways in the circular nut...
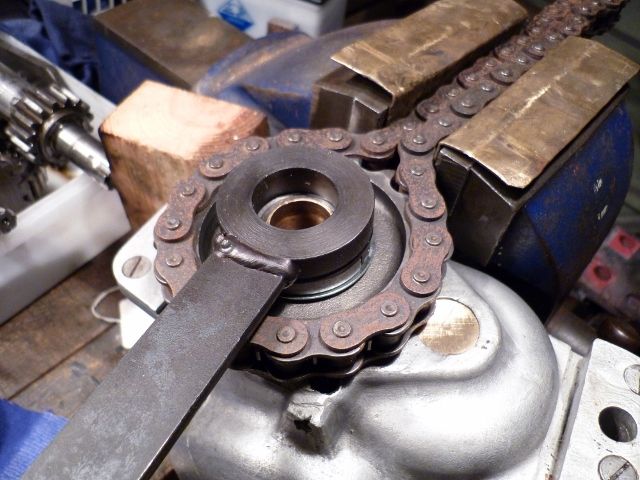
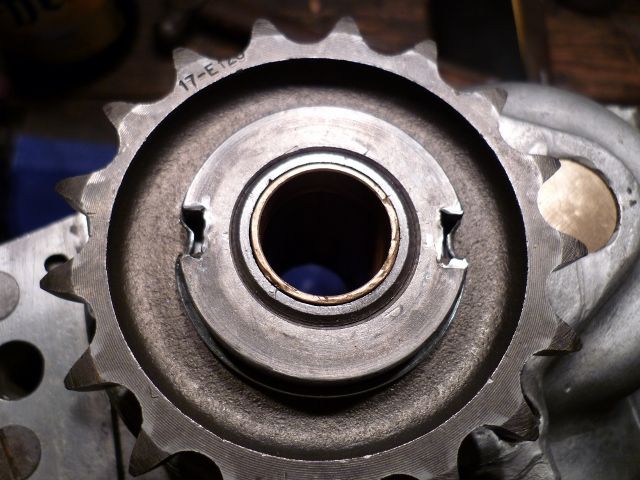
Pure bike porn eh?

. Got to have a short interlude now while I have me dinner. I hear the 'pinch method' works quite well if I've got you too close to the brink of your excitement thus far.
