Terry:
have you thought about orificing some extra oil over the cam bearings? This is the only spot I can think of that's in trouble on the (stock) 750 engine: the inner ones, in particular, get insufficient oil. The upper earing half has a collector opening where an overhead dripper or feeder would really help, especially at idle.
If someone were working with the hi-lift cams, adding a few drops to the lobes would help, too.
The wear on the rocker shafts can be removed far more simply than adding oil, like this: just install new shafts and DON'T install the little non-rotation bolts. Just use the center bolt for the bearing housing to hold it in place, like the K0-K1 did (beware: this bolt can only take 7.5 ft-lbs of torque before stripping the threads in the head!). It makes a slight mechanical noise appear, but letting it rotate also stops the wear. (130,000 miles can't be wrong, here!). This locked-in-place shafts first appeared in late K2 engines, and they wear on the bottom like crazy for lack of lube. Honda instaled the non-rotation bolts to reduce top-end clatter, especially behind the very popular Vetter fairings of the time. It stoped the clatter for about 5000-7000 miles, after which it was much worse from this shaft wear and the ovalled rockers. 
These engines are orificed in the head to reduce flow to the head while below 2000 RPM. Honda did this to preserve lots of oil for the plain bearings on the crankshaft. I guess that part was just so much more expensive, it was to be protected at all costs. The tradeoff, of course, is the loss of lube above, starting at the center 2 cam bearings, then working its way outward after about 1 minute of hot idle.
G'Day Mark, thanks for that mate, I love reading your posts, not only do you describe the problem, but you give us all a valuable history lesson about "why" Honda did this, and what the "fix" is, from someone who was actually there, with no BS, either. A refreshing change.............
When I pull my wicked 836 race engine apart to install the APE crank, I'm gonna remove those little rocker shaft screws, it's already pretty noisy with the Megacycle 125/75 cam and 5 thou valve clearances, so a little more will only add to the music that that engine already makes, ha ha!
I need an AC/DC TIG welder, then I'll certainly add some oil ports over the cam when I make my race engine valve covers with cam tower hold downs, but at the moment (having just paid out 1500 bucks this week for two lots of car registrations and a set of tyres for my Ford, and 1400 bucks for my mortgage) the TIG is still at arms length, and anyway, I'll need to teach myself to use it, once I manage to scrape together the dough.........
So for the time being, I'm still working on feeding the oil in via the exhaust side rocker inspection covers, because it'll be spraying oil rather than dripping it, the oil will hit the top of the rockers and exhaust valve spring caps, which will help to propel the oil all around the inside of the valve cover, so everything should get a mist of oil.
Last weekend I spent making oil cooler adapters and entertaining relatives, but I did make a start, I turned up a special oil cooler adapter with 3 ports, specifically for the top end oiler. I could have tapped into the bottom of one of my old Lockhart adapters, but I just didn't like how it was gonna look, so instead, I made my own.
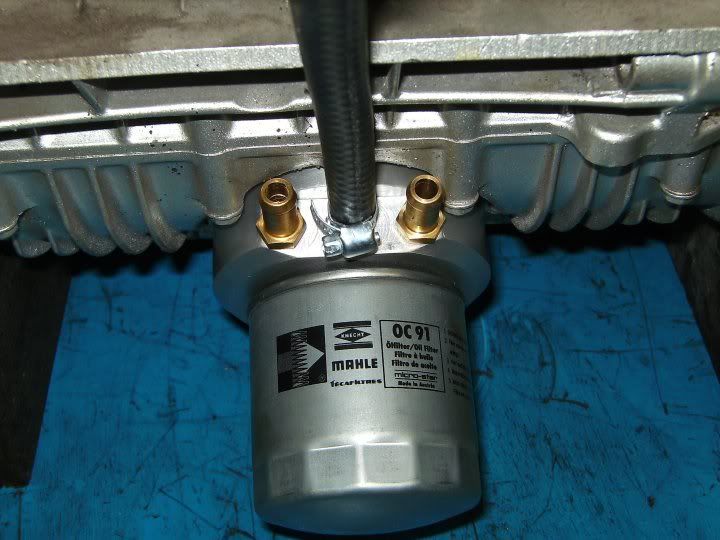
During the week I went to a hydraulic hose place and bought some cloth braided, steel reinforced, high pressure hot oil line, they said it'd fit over my 1/4" barb fittings, but they're full of #$%*, it's way too tight, and probably unnecessary anyway, so I've wasted another 30 bucks. I bought some shiny 1/4" ID braided stainless steel covered hose from a nice bloke on EBay in the US, so when that arrives, that'll have to do.
Yesterday I stalled going out to the garage as long as I could because it's freaking cold here at the moment, we've had rain, hail, and (in the hills where Steve K0 lives) snow! Anyway, I shamed myself into getting among the tools, and the first thing I did was measure the "oil restrictor" drilling in that K0 head you sent me (thanks mate) and was surprised that the hole size is less than my smallest available drill bit, 1.5mm.
I thought about going to the store to buy some smaller bits, but decided against it as the rain was pisssing down, and decided on the 1.5mm drill bit. Now, I'm using 1/8" BSPT fittings threaded into some old "chopper" style finned inspection covers, the benefit being that the fittings will sit further back from the rockers, allowing more "atomisation" of the oil, not to mention giving it a bit more clearance, I've seen damage on the insides of some stock OEM inspection covers where an owner has used a big cam and part of the "tapping" was the rocker arm contacting the cover.
Anyway, I've tapped the insides of the fittings and made up some "restictors" by drilling brass screws, threading and loctiting them inside the fittings, cutting off any excess, and countersinking them. It sounds easy I know, but my lathe is one big mother with a 40" bed and 18" swing, so a 6mm screw wouldn't sit in the 3 jaw chuck, and if it did and I tried to tighten it, it'd just mash the threads.
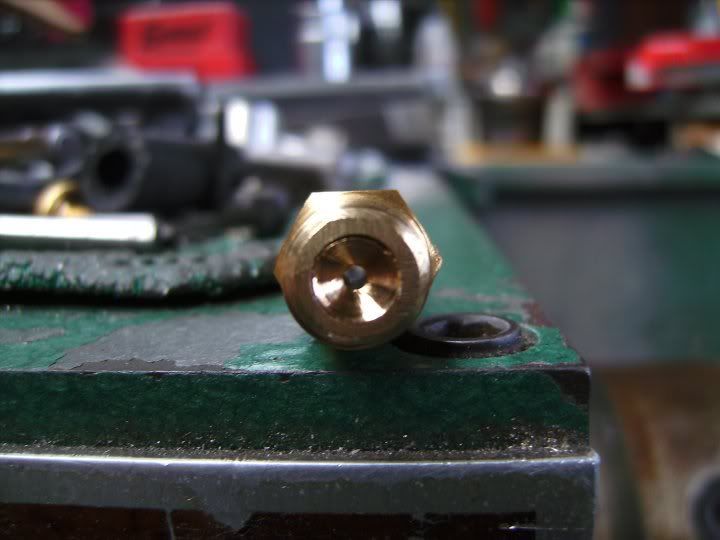
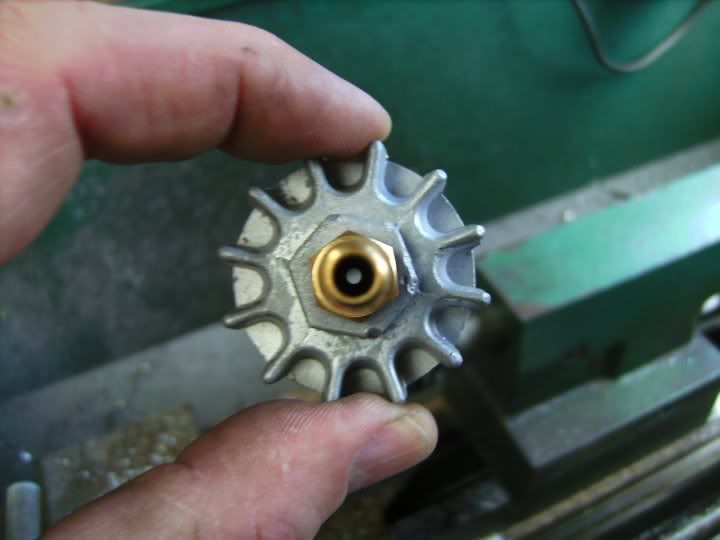
Hmmnnnn, easy enough, I found a piece of 1 1/2" brass bar (bronze actually, left over from making some swingarm bushes) and drilled and tapped it for the screw, so that way I could chuck it in my lathe, and drill it. Next problem, my 3/4" drilling chuck is way too big for a 1.5mm drill bit. Bugger. Now I've got a couple of "El Cheapo" Dremel knockoffs, so I went thru the collection of drill collets, and found one that would hold my little drill bit, so I then had to machine up a "collet chuck" so I could secure the drill bit in my drill chuck. Phew............
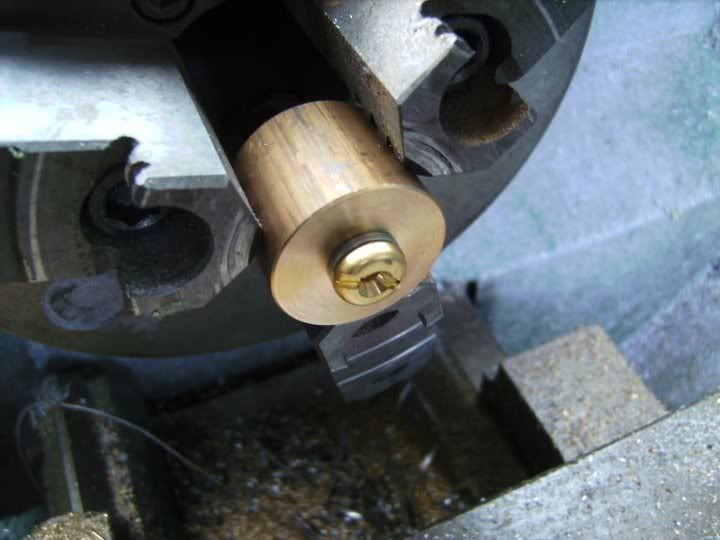
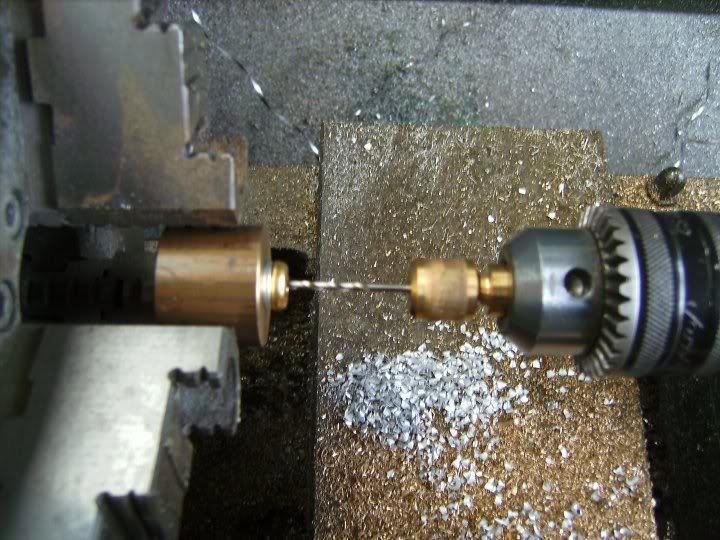
Steve K0 rang to tell me he's found me a set of K1 engine cases (geez he's a good bloke!) and I yakked to him for about half an hour, then the wife wanted me to drive her to the supermarket to get some groceries, (and I sneaked around to a bar and lost 30 bucks in a poker machine while drinking watered down Bourbon, but that's another story........) then I went to the hardware store to buy some "Simple Green" BBQ and Grill cleaner and some micro fiber cloths, but forgot the 1mm drill bit! Oh well................
I'm taking the fam out to see a movie today ("Taken" with Liam Neeson) but I'll get some more machining done before that, I need to make the other "restrictors" up, finish the manifold and mounts, bead blast the 30-odd years worth of crud off the rocker inspection covers, and drill and tap them for the fittings. It's doubtful that I'll actually get the kit mounted on my K0 today, but I'll set it up on my K2 engine and take some pics so you can see what I'm doing. Stay tuned! Cheers, Terry.
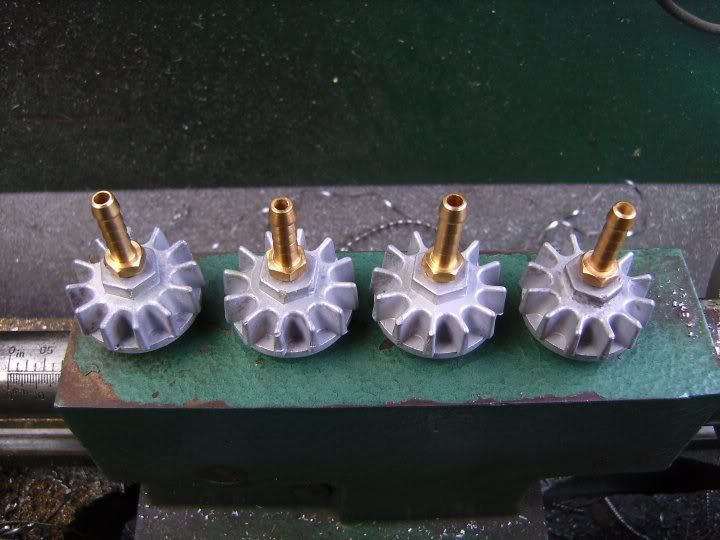
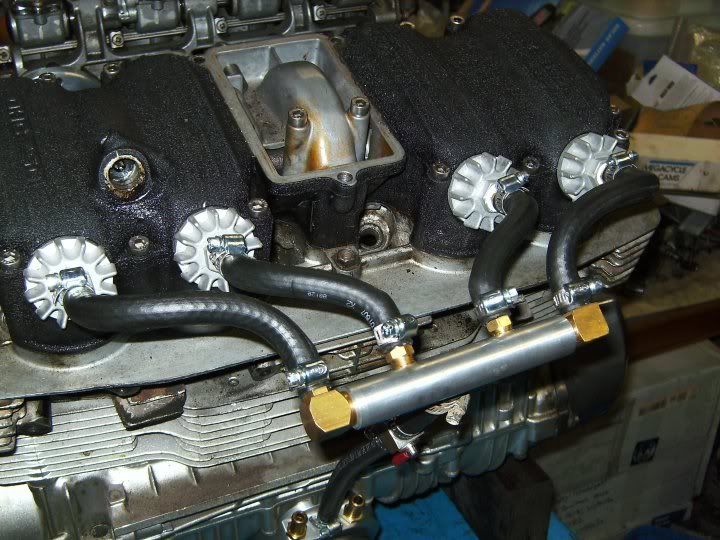