Day 41 update:
Yesterday my order of silver-colored powdered paint (sample size, 2 oz) came in from Columbia Coatings. So I headed down to TechShop this evening to sign up for a month of use. I promptly shot three small strips of aluminum with one color each so I could compare and decide on which one would become the frame color. I took a picture of the results; however, it's next to impossible to tell the difference from the resulting image so it's of no use to share. Instead, I'll just point to the images directly from Columbia's website. I've pretty much decided on the first one.
Silver Metallic Urethane:

This one came out nice, with a decent gloss and not the overdone metal flake look.
Anodized Aluminum:

This was very matte, requiring a clear coat to get any kind of gloss. It would make an
excellent color for the engine, however. I think the only problem with powder coating the engine is the lack of thermal conductivity in the paint. That is, they're most often insulators. Not good for an air-cooled engine to be coated in a blanket.
Wheel Silver:

This one had a glossy sheen; however, it screamed "flat gray" and just didn't do anything for me.
Of course, the colors you see on their website aren't perfect matches to what you get in reality. Which is why I ordered small bottles to try them out myself. I also ordered a bottle of
Sheen Black TGIC, which was advertised as having 80% gloss. Decided to hit up the battery box, air duct mount plate, and cable protector plate with it. Here are the results!
This one is done, as it is completely coated and looks good:
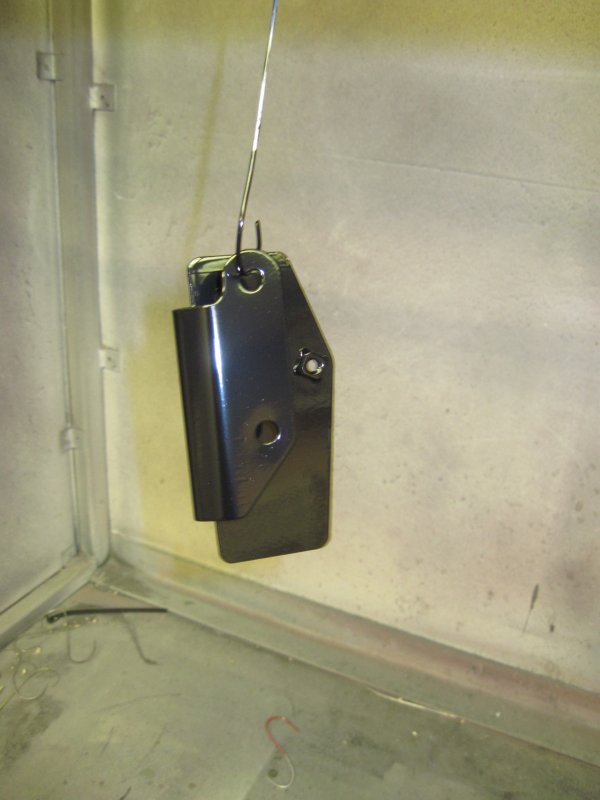
The battery box has a couple small thin areas, and I accidentally brushed the powder with my glove in one spot while transferring it to the oven

So I'll be doing a second coat... just couldn't do it tonight as they close at midnight and I ran out of time.
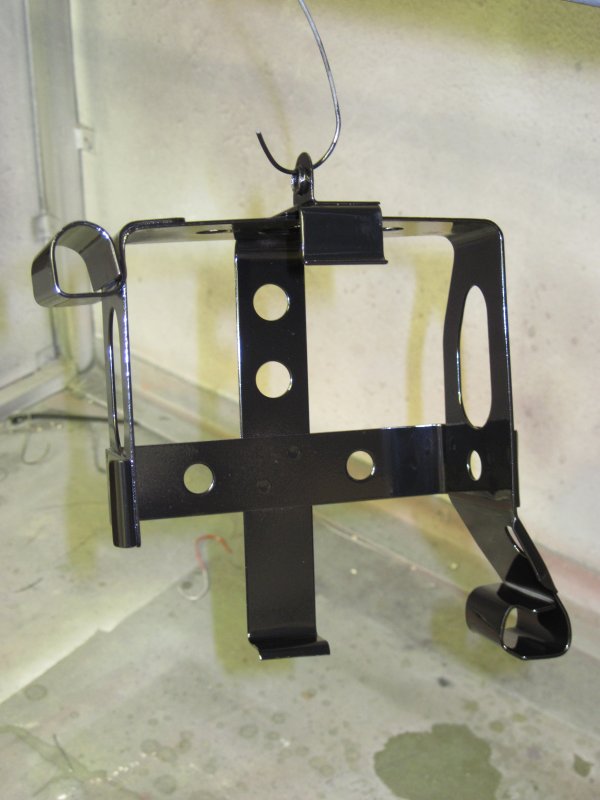
The air duct mount is also basically finished, although I might hit it up again, as the edge perimeter could use a little more coverage:
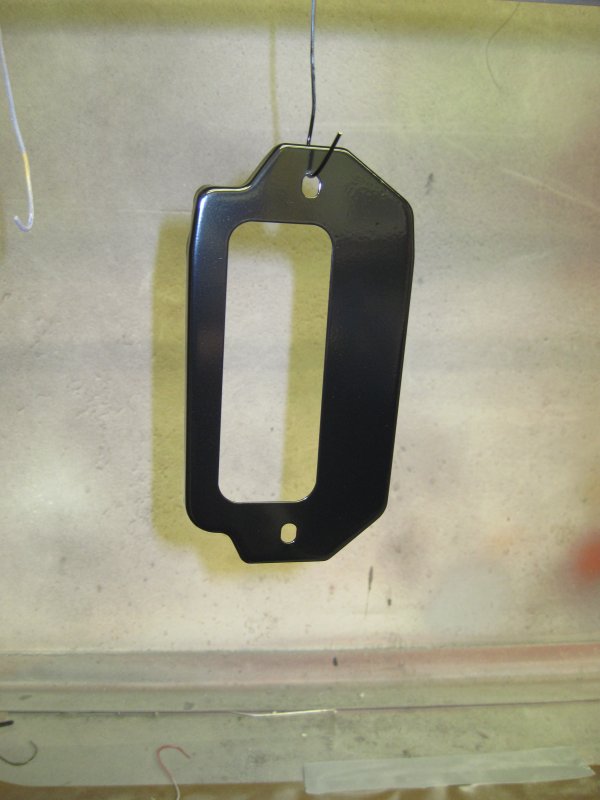
All in all, I'm really pleased with the results. Practice will make perfect, but it's pretty hard to screw up powder coating too horribly. The curing temp and duration is specified by the manufacturer and written right on the bottle. The hardest part is getting into the tight crevices; the paint won't always go exactly where you want it to (or think it will go). Once it finds an outlet for the high potential, it clings there tightly. This was most noticeable on the battery box. I think a second coat will get it all, as those thin areas have more metal exposed and thus the paint should stick there preferentially.
I'll close with some pics of the facilities at TechShop:
Powder coating gun:
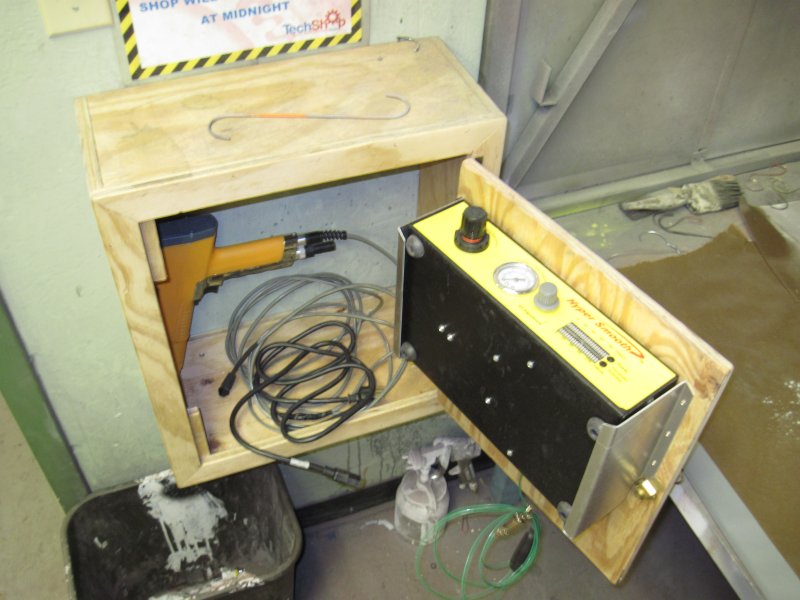
20" x 20" x 20" oven (smells pretty bad):
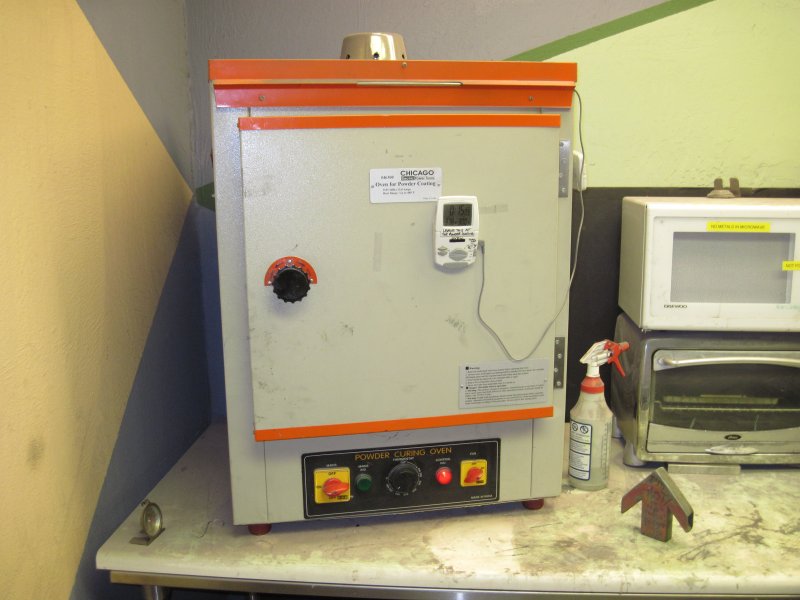
Standard upright sandblasting cabinet:
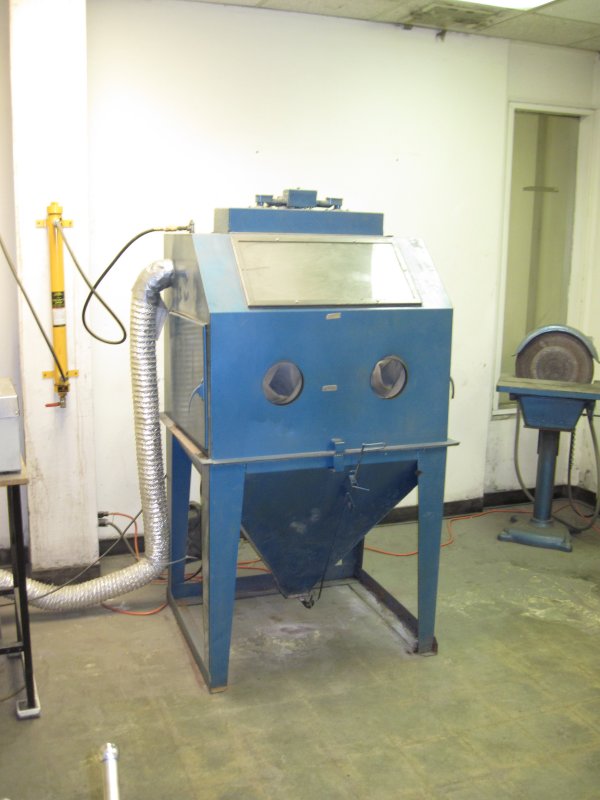
I also discovered that they have a laser cutting machine. Which means I can fabricate new gauge face plates out of acrylic in order to replace the stock ones (and not disturb them). Just have to come up with a drawing to specify the correct dimensions, then let the laser go to town, so to speak. Make up a couple new decals to lay down on top, and they're done!