your MOM is cheap and easy!

sorry, just had to get that out of my system.

anyway... homemade valve adjust tool...
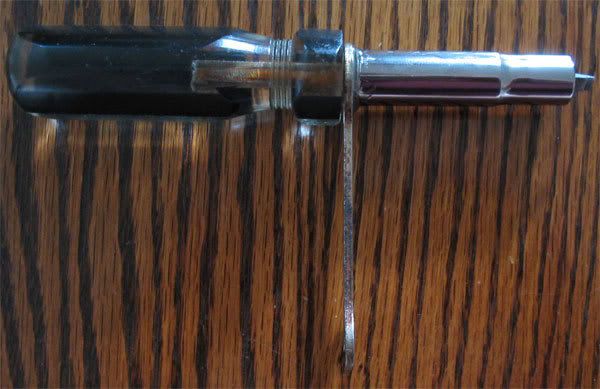
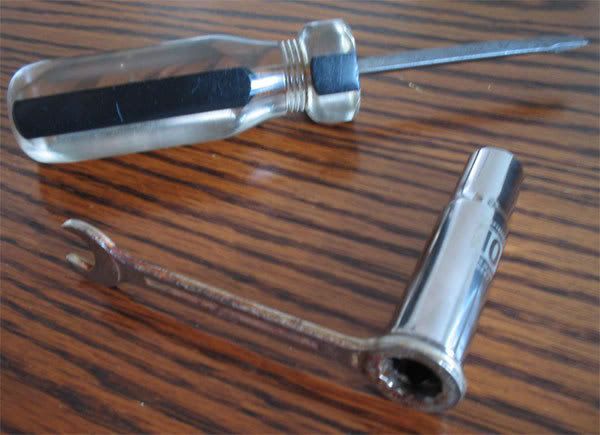
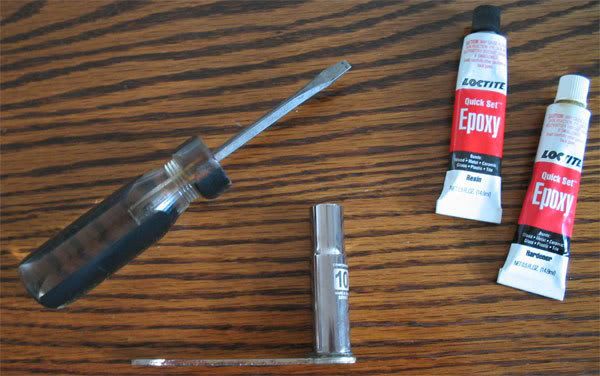
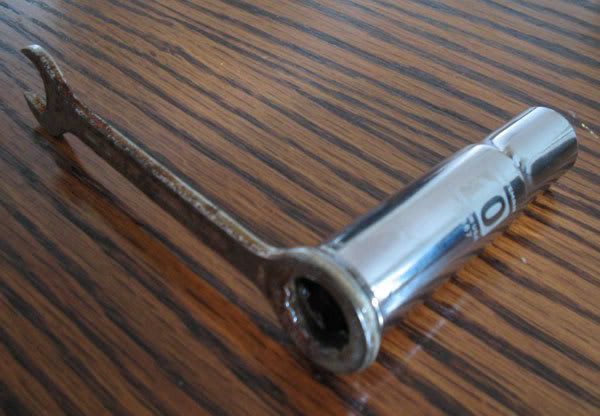
1- 10mm deep socket (12 point works best for this particular application)
1- old, small, least used size, box end wrench (keep it small, too much torque on the lock nuts is bad... ideal size is roughly the same size as the 3/8 square drive in the socket)
1 old screwdriver that will fit thru 3/8" square drive in socket
1- loctite epoxy... this stuff is strong! i like this brand since it is clear, unlike jbweld.
first, make sure to scar up the mating surfaces a bit for good adhesion
mix epoxy
dip both mating surfaces in epoxy, wait a minute or two then join the two pieces
let cure for about 15 minutes
then really go at it w/ more epoxy, i tried to completely encase the end of the box end, then also took the epoxy down inside the box end and socket drive... this should ensure that torque applied to the new tool won't just snap it apart. w/ the 12 point box end and the square drive, the epoxy will mesh and hardens in those and just really won't let go at this point.
lastly, insert screwdriver or square bit driver and
ADJUST THOSE VALVES!

i had everything except the extra deep socket... not gonna give up one of the most important tools in my box w/out replacing it.

the craftsman 10mm was 4.99 at sears. can't beat a 5 dollar tool that was supposed to cost at least 3 times that and may or may not be in stock at only motorcycle shops.
i know, i know... i could've welded it and it would be even stronger... i would've except i have no welder, and now that its cured, i have 100% faith that the small amount of torque needed for the application will not be too much for the new tool. now, i probably wouldn't use it to break the nuts free, but its not really needed for that anyway.
just made it last night for use today... going out to give it a try.
